Morten Kjeldsen
Managing director and Research and Innovation manager, PhD
I investigate and develop new opportunities and solutions at FDB but also together with other parties. I contribute with my expertise to FDB’s existing products and services. I also engage in FDBs sales and marketing efforts.
For my engineering contributions I use 3D CFD and 1D CFD, Flomaster and LVTrans, for evaluation of system and component performance, and NI LabView for analysis of dynamic measurement data. I also strive to provide and deliver analytical or theoretical models for engineering tasks I approach.
Work Experiences
Numerous projects spanning a range of sizes, industries, and tools or approaches applied. The larger activities include
- DiffCon: Numerous projects. Project idea and project leader.
- LiTRo: Norwegian Research council and together with NTNU and Norwegian hydropower operators. Project idea and definition. Project leader.
- AFC4Hydro: EU Horizon 2020 project. Project definition and WP leader.
- Industrial PhDs: Project definitions and supervision.
- Subsea heat transfer: Engaged is tasks for Gullfaks, Aasgard and Ormen Lange.
Associate Professor at dept. of Energy and Process Technology, NTNU. Held the professorship in Fluid Power. Main responsibility for one PhD student, several Master students and Master level course on Industrial Fluid Power. 50% appointment started July 2009 until June 2011.
Dr. Ing. (Doctoral degree mechanical engineering)”Cavitation in Hydraulic Machinery” Norwegian University of Science and Technology (NTNU), Trondheim, Norway. Study on interaction between hydraulic transients and the cavitation phenomenon.
Education
- Dr. Ing. ”Cavitation in Hydraulic Machinery” , NTNU (1996)
- Master of Science in Mechanical Engineering, NTNU (2011)
Skills
Professional Skills
- Flomaster
- Ansys CFD
- NI LabVIEW
- LVTrans
- Acad
Publications
Cavitation highlights
- Marschall, Mørch, Keller & Kjeldsen “Cavitation inception by almost spherical solid particles in water”, Physics of Fluids, Vol.15, no2, 2003. Conceptual idea by MK. Laboratory works in TUM Obernach, Germany (Marschall & Keller) and DTU, Lyngby, Denmark (Mørch).
- Kjeldsen, Arndt & Effertz “Spectral Characteristics of Sheet/Cloud Cavitation”, ASME- JFE, 2000. Summary of work on transient loads from cavitation.
- Escaler, Ekanger, Francke, Kjeldsen and Nielsen “Detection of Draft Tube Surge and Erosive Blade Cavitation in a Full-Scale Francis Turbine”, ASME-JFE, 2015. Covering Industrial PhD (Ekanger) and work on developing the FDB cavitation monitoring system.
Industrial relevant publication
- Analysis using empirical relations, 1D system simulation tools (Flomaster) and 3D heat and flow analysis tools. See: Transient modeling of riser load control: Technology qualification using CAE and physical tests. CAE Conference 2016. Full copy available upon request.
Portfolio
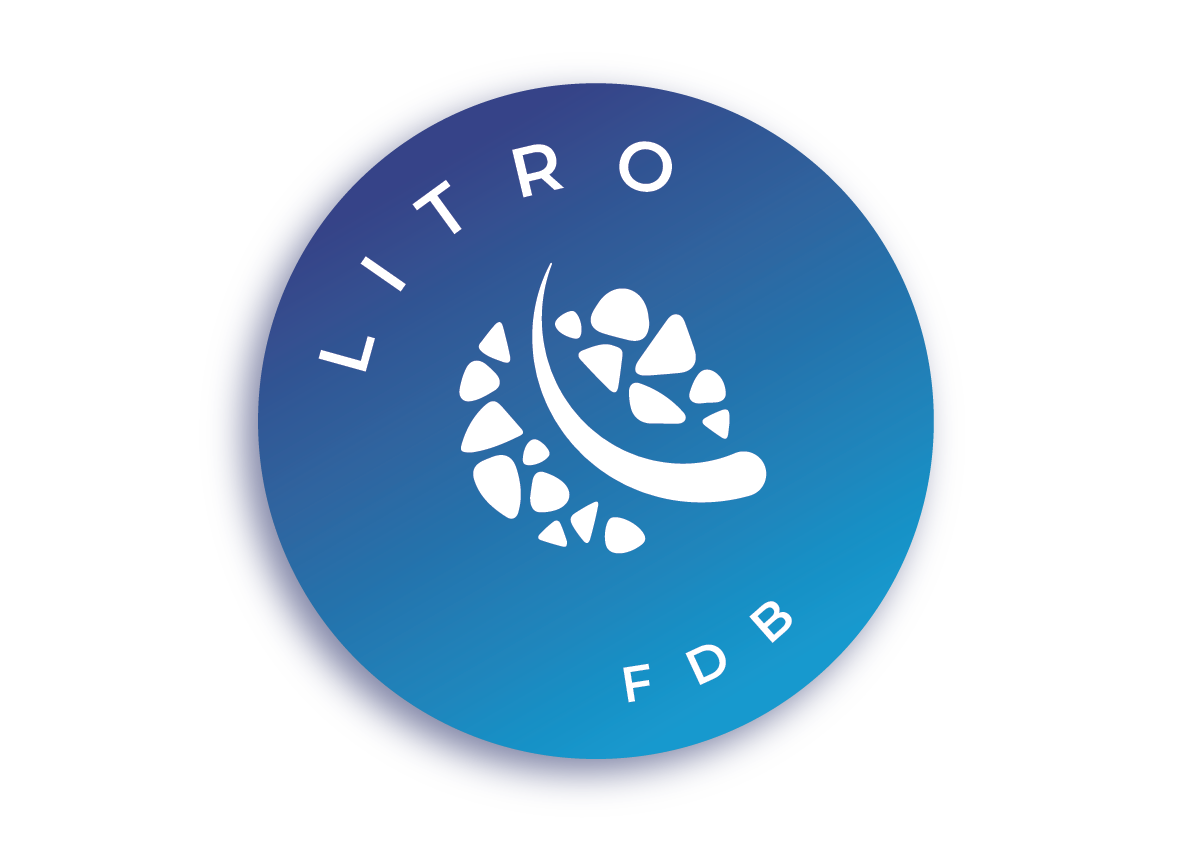
Litro
NTNU/FDB, 2019
LiTRo is a joint research project with the Norwegian University of Science and Technology (NTNU). It consisted of the design and manufacturing of a mobile test rig for investigating the Lifting and Transportation mechanisms of rocks and sand (hence the name: Lift and Transportation of Rocks).
The test rig was designed as a closed loop pump system, with a lower reservoir, a surge shaft, and upper reservoir, and a transparent rectangular test-section placing rock and sand specimens. The rig also included a measurement cabinet that monitored and measured rig parameters such as flow rate, pressure, surge shaft level, and valve positions. The rig is built within a large shipping container, with the upper reservoir residing on top of the container when rigged up for use. The surge shaft also protruded from the top of the container, and the pipe section upstream the test section exited and reentered the container, allowing for a long straight section for achieving fully developed flow.
My role:
Project idea and definition.
Head analysis...
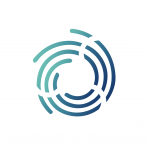
DiffCon
NTNU/FDB, 2004
Draft tube water injection system for the mitigation of pressure pulsations.
Together with Norwegian power companies, FDB has been developing DiffCon since 2004. This partnership has continued and DiffCon is now being developed by FDB in collaboration with Statkraft. The basic principle is that the system tries to control the total rotation within the hydro turbine draft tube. The total rotation is defined as the integral value of the product of tangential and axial velocity over the cross-sectional area. The flow becomes naturally unstable for given load settings and where large vortices and pressure pulsations dominate. By injecting water at high speed into the draft tube, this instability is mitigated and resulting in a calmer machine.
My role:
Numerous projects.
Conceptual idea and project leader.

AFC4Hydro
EU Horizon 2020
The overall objective of the AFC4Hydro research project is to design, implement and validate in full-scale water turbine an active flow control system that permit to increase efficiency and reduce the dynamics loads on the structure at any off-design operating conditions and during transient operations.
Specifically, the system will modify the draft tube flow field to mitigate or supress the pressure fluctuations induced by the vortical flow which limits the operation of actual hydraulic machines. Special attention will be given to the flow instability leading to the formation of the vortex rope in the draft tube.
A combination of two innovative technologies will be used in the draft tube:
- injection of pulsating momentum (IPM) with a specific frequency, amplitude and phase by means of actuators;
- injection of continuous momentum (ICM) in the form of water jets with controlled speed and orientation directed against the swirling flow.
The IPM handles the problem at its source, while the ICM is the remedy when the problem arises. A structural health monitoring (SHM) system will be developed to continuously evaluate the performance of the turbine in real time and used as a feedback to adjust the flow control strategy with a specifically designed Controller. This closed loop configuration will permit to enhance the stability of the flow and decrease the level of unsteadiness also during transients such as ramp up and ramp down.
My role:
Project definition and WP leader.
Other Projects
- Industrial PhDs: Project definitions and supervision.
- Subsea heat transfer: Engaged is tasks for Gullfaks, Aasgard and Ormen Lange three major subsea projects on the Norwegian continental shelf. 3D CFD and development of models for use in other SW. Experimental program for investigating the effect of gas-carry-over on liquid pump boost.
- Associate professor @NTNU. Main responsibility for one PhD student, several Master students and Master level course on Industrial Fluid Power.
- Associate professor @NTNU. Lectures and MSc supervision. Research and hydraulic design for tidal turbine prototype by Hammerfest Strøm. Installed in Kvalsundet in Northern Norway.
- Head experimentalist at the UMN St.Anthony Falls Laboratory cavitation tunnel, and for a ONR (Office of Naval Research- US Navy) funded studies on dynamics of cavitation.