Elia Antoniali
Mechanical Engineer, MSc.
Passionate Mechanical Engineer with experience in the full chain of product development and focus on design, product assembly, test and installation.
At FDB, I contribute to the development, integration and testing of a modernized, multi-degrees of freedom water injection system aimed at improving the efficiency of hydropower plants.
Work Experiences
- Mechanical Engineer – Flow Design Bureau AS
[Nov. 2020 – Today]
- Mechanical AIT Engineer – Airbus Defence and Space GmbH
[Jun. 2023 – Today]
- Test Engineer (Internship) – Flow Design Bureau AS
[Jun. 2020 – Nov. 2020]
Education
- Technische Universität Berlin – MSc. Global Production Engineering [Ott. 2021 – Nov. 2023]
- Università degli Studi di Padova – BSc. Mechanical Engineering [Ott. 2016 – Mar. 2020]
Skills
Professional Skills
- MS Office (Visio, Access)
- SolidWorks
- CATIA V5
- Straus7
Portfolio

AFC4Hydro
& DiffCon
EU Horizon 2020
The overall objective of the AFC4Hydro research project is to design, implement and validate in full-scale water turbine an active flow control system that permit to increase efficiency and reduce the dynamics loads on the structure at any off-design operating conditions and during transient operations.
Specifically, the system will modify the draft tube flow field to mitigate or supress the pressure fluctuations induced by the vortical flow which limits the operation of actual hydraulic machines. Special attention will be given to the flow instability leading to the formation of the vortex rope in the draft tube.
A combination of two innovative technologies will be used in the draft tube:
- injection of pulsating momentum (IPM) with a specific frequency, amplitude and phase by means of actuators;
- injection of continuous momentum (ICM) in the form of water jets with controlled speed and orientation directed against the swirling flow.
The IPM handles the problem at its source, while the ICM is the remedy when the problem arises. A structural health monitoring (SHM) system will be developed to continuously evaluate the performance of the turbine in real time and used as a feedback to adjust the flow control strategy with a specifically designed Controller. This closed loop configuration will permit to enhance the stability of the flow and decrease the level of unsteadiness also during transients such as ramp up and ramp down.
My role:
➜ Designed and developed a modernized water injection system (ICM) with multi-degrees of freedom for efficiency improvement reduction of dynamic load on Francis based turbines.
➜ Definition of product documentation (BOM, FEA reports, PFMEA, User Manual, SOP for manufacturing and safety of installation).
➜ Successfully completed integration, validation tests, and installation of the ICM on R&D laboratories (Luleå University’s hydraulic lab and Vattenfall’s R&D center Älvkarleby) and hydropower plants (Vattenfall’s Porjus U9 and Statkraft’s Svorka).
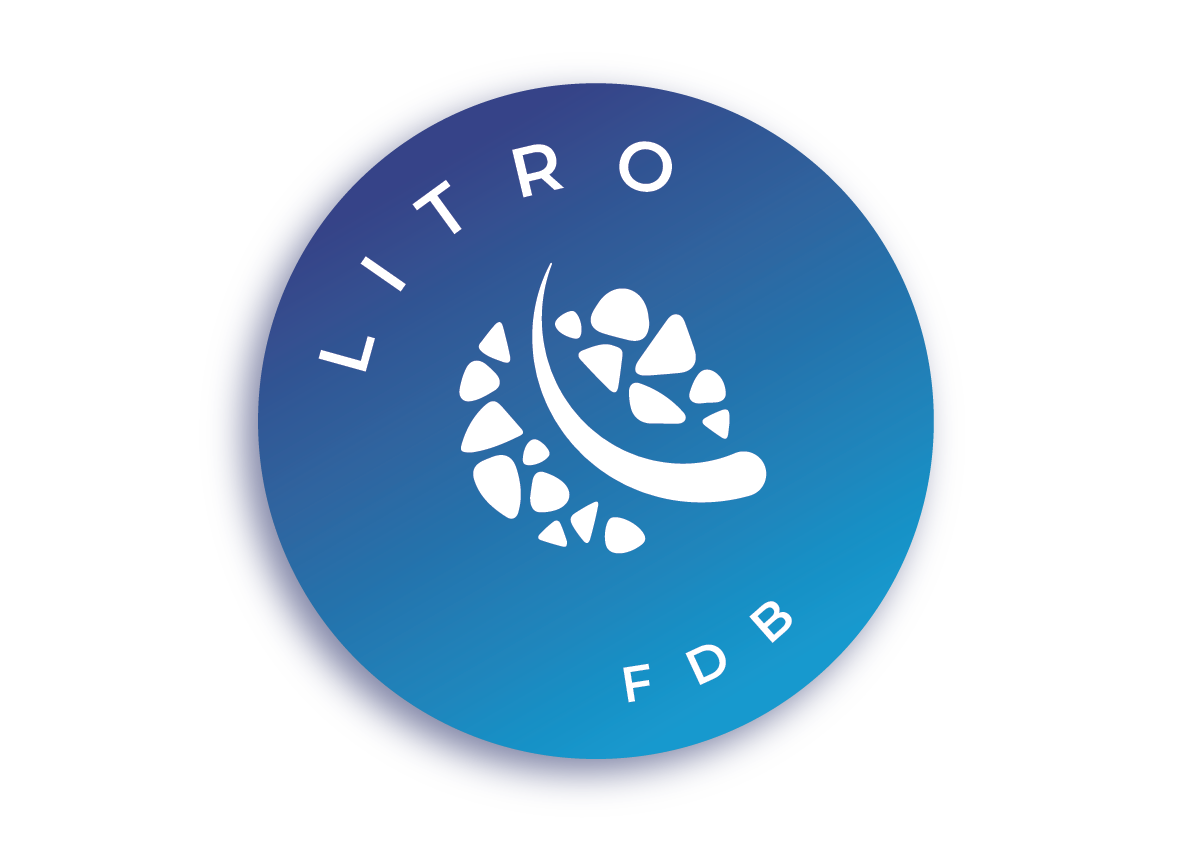
Litro
NTNU/FDB, 2019
LiTRo is a joint research project with the Norwegian University of Science and Technology (NTNU). It consisted of the design and manufacturing of a mobile test rig for investigating the Lifting and Transportation mechanisms of rocks and sand (hence the name: Lift and Transportation of Rocks).
The test rig was designed as a closed loop pump system, with a lower reservoir, a surge shaft, and upper reservoir, and a transparent rectangular test-section placing rock and sand specimens. The rig also included a measurement cabinet that monitored and measured rig parameters such as flow rate, pressure, surge shaft level, and valve positions. The rig is built within a large shipping container, with the upper reservoir residing on top of the container when rigged up for use. The surge shaft also protruded from the top of the container, and the pipe section upstream the test section exited and reentered the container, allowing for a long straight section for achieving fully developed flow.
My role:
➜ Assured production scheduling and led installation of the LiTRo test rig.
➜ Defined Standard Operation Procedures for the facility utilization while executed performance mapping and efficiency implementation.
➜ Coordinated on-site installation of the LiTro test rig.